모따기면의 형상을 정량적으로 정확하게 측정하는 방법
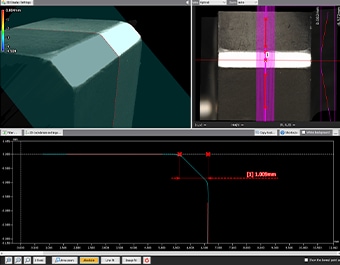
최근에는 금속뿐만 아니라 가볍고 강도 높은 CFRP(탄소 섬유 강화 수지)나 강화 유리 등을 재료로 한 부품·제품의 모서리(에지)를 모따기 가공해 모따기면으로 마무리하는 경우가 많습니다. 기어 등 접촉 부분이 있는 기계 부품의 에지 마모 방지는 물론 시계나 필기구, 스마트 폰이나 태블릿, 웨어러블 단말 등 사람이 닿는 제품에도 적용되는 경우가 있습니다.
고정도의 모따기 가공이 요구되는 부품의 경우 올바르게 가공되어 있는지를 확인하기 위해 높은 정도로 정량적인 측정이 필요합니다.이 페이지에서는 모따기면의 도면 표기 등의 기초 지식부터 고정도 가공을 실현하는데 빠뜨릴 수 없는 측정 과제와 해결 방법을 소개합니다.
- 모따기면이란?
- 모따기면의 도면 기재
- 모따기면 가공 깊이 계산 방법
- 모따기면 측정에서 기존 측정기의 과제
- 모따기면 측정에서의 과제 해결 방법
- 요약: 3D 스캔은 모따기면 측정의 비약적인 개선 · 효율화를 실현
모따기면이란?
강도가 높은 재료를 전단 가공이나 펀칭 가공했을 경우 가장자리가 매우 날카로워지므로 모따기 가공(에지 처리)을 실시합니다. 모따기 가공에는 여러 종류가 있으며 모따기 부분의 형상에 차이가 있습니다. 모서리를 대각선으로 절단하는 것을 「C 모따기」라고 합니다. 그 밖에도 모서리를 둥글게 가공하는 「R 모따기」, 미세하게 조정한 가공을 「실 모따기」등이 있습니다.
모따기면의 도면 기재
모따기면은 종종 도면에서 「C5」나 「C10」과 같이 「C」와 「숫자」로 표시됩니다. 「C」는 chamfering(모따기)을 의미하며 일반적으로 45도의 모따기면을 의미합니다. 그 옆에 붙는 숫자는 잘라내는 가장자리의 치수(길이: mm)입니다. 즉, 변의 치수(길이)로 교차하는 직각 이등변 삼각형으로 잘라낸 「45도의 모따기면」을 의미하고 있습니다. 예를 들면 「C3」의 경우의 도면 표기와 가공 내용을 나타냅니다.
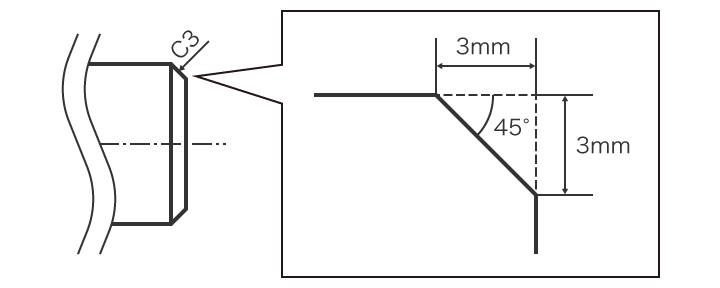
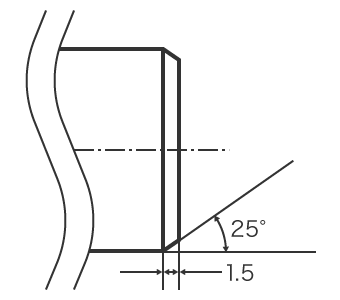
일반적으로 모따기면의 각도가 45도가 아닌 경우에는 각도와 치수로 표기합니다. 예를 들어 모따기면의 각도가 25도이고 모따기할 부분의 변의 길이가 1.5mm인 경우는 아래와 같이 나타냅니다.
모따기면 가공 깊이 계산 방법
예를 들어 가장자리의 45도 각도에서 공구 또는 가공 대상 물체를 맞추고, 절삭하여 모따기면을 취하는 경우, 가장자리부터의 깊이를 계산하는 것으로 어느 정도 깊게 깎으면 되는지를 알 수 있습니다.
깎고 싶은 깊이를 「D」로 합니다.「C1」의 경우 아래의 계산식으로 깎는 깊이를 구할 수 있습니다.
- D=1.0÷√2≒0.7(mm)
- 구하려는 깊이 D는 1mm×1mm의 변으로 끼인 직각 이등변 삼각형을 반으로 한 긴 변 1.0의 직각 이등변 삼각형의 짧은 변에 해당합니다.
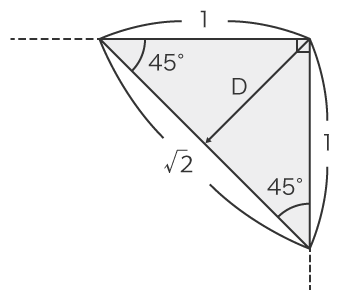
직각 이등변 삼각형의 변의 비율은 1: 1: √2입니다.
단순화하면 다음과 같습니다.
- D≒0.7(mm)
- 이것을 기억하면 예를 들어 「C4」일 때는 D×4≒2.8과 같이 45도 방향에서 에지를 깎는 깊이를 간단하게 구할 수 있습니다.
모따기면 측정에서 기존 측정기의 과제
모따기면 가공으로 원하는 치수(공차 내)·형상을 얻었는지 확인하는 것은 매우 중요합니다. 모따기면은 입체적인 형상이므로 고정도 및 정량적인 3D 형상의 측정이 요구됩니다.
그러나 기존의 3차원 측정기나 윤곽 형상 측정기, 버니어 캘리퍼스, 측정 게이지 등을 이용하여 측정하는 경우 정확한 측정을 실현하기에는 난이도가 높은 등, 다양한 과제가 있었습니다.
3차원 측정기에서의 모따기면 측정 과제
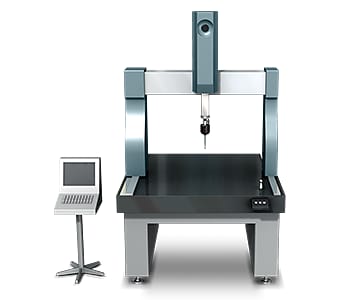
일반적으로 3차원 측정기에서는 대상 물체의 3~6점에 접촉자를 맞추어 가상면을 작성하여 모따기면을 측정하지만 다음과 같은 과제가 있습니다.
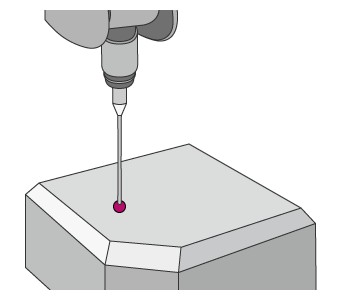
- 예를 들어 모따기면 부분의 면적이 1mm2로 작으면 프로브를 사용하여 가상 면을 만들고 정확하게 측정하기는 매우 어렵습니다.
- 작은 부분의 3차원 형상을 측정하는 경우 3차원 측정기에 CAD 도면을 불러오는 등의 방법을 고안해야합니다. 일정 수준의 숙련도가 필요한 측정기이기 때문에 CAD 도면을 이용하기 위해서는 더욱 복잡하고 난이도가 높은 조작이 요구됩니다.
이와 같이 현장의 모든 사람이 정확하게 측정할 수 있는 것은 아니라는 것이 큰 과제였습니다. 또한 가상면의 교차점에서 모따기면을 측정하므로 실제 모양을 반영할 수 없습니다.
윤곽 형상 측정기에서의 모따기면 측정 과제
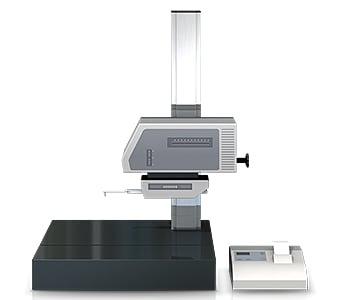
윤곽 형상 측정기에서는 측정하려는 모따기면의 형상에 대해 수직 방향으로 정확한 측정 라인을 취해야 합니다. 그래서 다음과 같은 과제가 있었습니다.
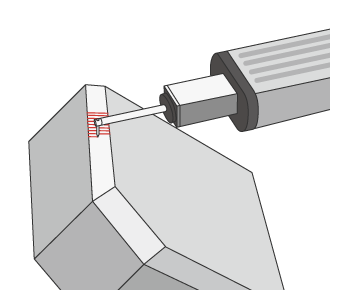
- 시료를 지그에 고정하거나 레벨링 등의 작업에 시간이 걸립니다.
- 정확한 레벨링을 위해서는 윤곽 형상 측정기에 관한 지식이나 스킬이 필수입니다.
- 원하는 대로 바늘을 통과시키는 작업은 매우 어렵고 미묘한 바늘의 어긋남이 측정값 편차의 원인이 됩니다.
모따기면 버니어 캘리퍼스와 게이지에서의 모따기면 측정 과제
모따기면 버니어 캘리퍼스와 모따기면 측정 게이지 등 핸드 툴은 매우 간편한 측정이 가능합니다. 그러나 측정 오차의 발생이나 측정값이 어긋나는 요인이 여러가지 있습니다.
예를 들면 버니어 캘리퍼스나 게이지는 손으로 측정 부분을 누르는 힘(측정력)이나 측정 부분의 편차 등 사람에 따라 측정 정도가 다릅니다. 그 결과 측정값에 편차가 발생하여 정량적인 측정이 어려워집니다.
모따기면 측정에서의 과제 해결 방법
기존에 사용되고 있는 일반적인 측정기에서의 과제를 재검토하면 어떤 공통점을 알 수 있습니다. 그것은 입체적인 대상 물체·측정 부분을 점이나 선으로 접촉하면서 측정한다는 것입니다.
이러한 측정 과제를 해결하기 위해 KEYENCE에서는 원 샷 3D 형상 측정기「VR 시리즈」를 개발했습니다. 대상 물체의 3D 형상을 비접촉 방식을 이용하여 면으로 정확하게 포착할 수 있습니다. 스테이지의 대상 물체를 최고 속도 1초만에 3D 스캔하여 3차원 형상을 고정도로 측정할 수 있습니다. 따라서 측정 결과의 편차 없이 순간적으로 정량적인 측정을 실시할 수 있습니다. 구체적인 장점은 다음과 같습니다.
장점 1: 편차가 생기지 않는다
스캔하여 취득한 3D 형상 데이터에 PC 화면상의 다양한 보조 툴을 사용함으로써 임의의 위치에 정확하게 수직인 프로파일 선을 그릴 수 있기 때문에 측정 결과에 편차가 생기지 않습니다.

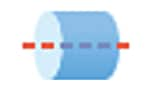
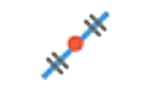
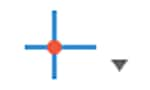
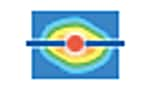
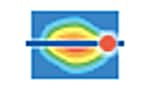
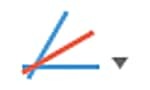
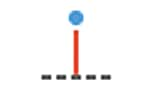
풍부한 보조 툴로 정확한 측정이 용이
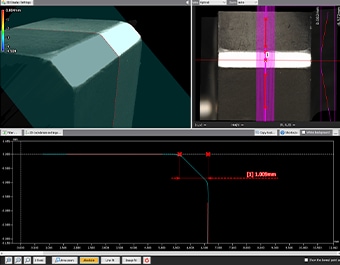
일단 대상 물체를 스캔하면 과거에 측정했던 부분과는 다른 부분의 프로파일(단면 형상)을 측정하는 것도 가능합니다. 일부러 동일 개체를 다시 준비하여 재측정할 필요는 없습니다. 또한 과거의 데이터를 활용하여 로트나 가공 조건, 재료 등이 다른 동일 형상의 워크와의 차이를 쉽게 확인할 수 있습니다.
장점 2: 위치에 상관없이 스테이지에 올리기만 하면 OK
측정에 필요한 작업은 대상 물체를 스테이지에 놓고 버튼을 누르기만 하면 OK. 엄격한 위치 결정 등의 사전 준비가 불필요하므로 측정기의 지식이나 경험이 없어도 즉시 고정도로 측정할 수 있습니다.
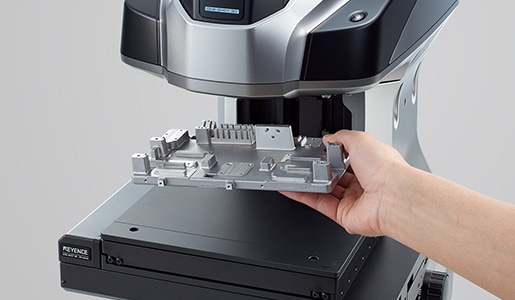
기존 측정기와 달리 스테이지에 놓은 대상 물체의 특징을 추출하여 자동으로 위치 보정할 수 있습니다. 지금까지 많은 노력과 시간이 걸렸던 엄격한 위치 조정이 필요하지 않습니다. 그 때문에 측정 작업이 특정 작업자만 할 수 있지 않고 익숙하지 않은 분이라도 간단·순식간에 측정할 수 있습니다.
장점 3: 고속 및 고정밀 측정
원 샷 최고 속도 1초만에 측정이 완료됩니다. 기존의 측정기로는 측정에 많은 시간이 소요되었기 때문에 N수를 늘릴 수 없었지만 VR 시리즈를 이용하여 N수를 큰 폭으로 늘릴 수 있습니다.
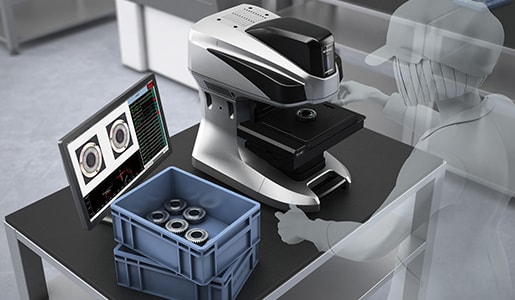
대상 물체를 빠르고 간단하게 측정할 수 있기 때문에 고정도의 3D 형상 측정을 개발하거나 시도하는 것은 물론 샘플링 검사나 소형 로트·고부가가치 제품의 전수 검사에 활용할 수 있습니다. 불량품의 유출을 억제하는 것은 물론 간단한 조작으로 리포트도 제작할 수 있기 때문에 불필요한 공정 수를 들이지 않고도 고객의 신뢰를 얻을 수 있습니다.
요약: 3D 스캔은 모따기면 측정의 비약적인 개선 · 효율화를 실현
고속 3D 스캔을 통해 비접촉으로 대상 물체의 정확한 3D 형상을 순간적으로 측정할 수 있는 「VR 시리즈」는 기존 측정기의 과제를 해결할 수 있습니다.
- 사람에 의한 측정값의 편차를 해소하여 정량적인 측정이 가능합니다.
- 위치 결정 등의 작업 없이 스테이지에 대상 물체를 놓고 버튼을 누르기만 하면 되는 간단 조작을 실현. 특정 작업자만 측정 업무를 할 수 있는 문제를 해소합니다.
- 간단·고속·고정도로 3D 형상을 측정할 수 있기 때문에 단시간에 많은 대상 물체를 측정할 수 있어 품질 향상에 도움이 됩니다.
그 외에도 과거의 3D 형상 데이터나 CAD 데이터와의 비교, 공차 범위 내에서의 분포 등을 간단하게 분석할 수 있기 때문에 제품 개발이나 제조 경향 분석, 샘플링 검사 등 다양한 용도로 활용할 수 있습니다.