열처리 후의 변형 측정 과제의 해결
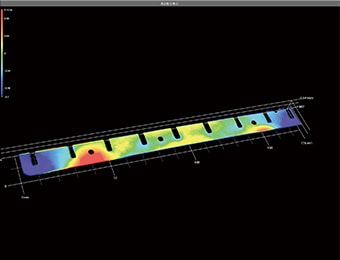
일반적으로 「열처리」란 재료나 제품에 열을 가하는 처리입니다. 금속 열처리에 의한 재료 가공이나 식품 등의 가열 살균 처리 등이 포함되지만 여기에서는 금속 열처리에 의한 변형에 대해 고찰합니다. 열처리에 의한 변형은 각재나 봉재에서는 축소나 휨이라고 하는 단순한 변형이 되지만 복잡한 형상의 제품인 경우에는 3차원적인 변형이 되며, 그 측정에는 고도의 기술이 필요하게 됩니다.
여기에서는 주로 철·강 소재의 조직을 제어하고 성능을 향상시키기 위해 실시하는 열처리에 의한 변형의 기초 지식을 설명하고 나아가 변형의 측정 과제와 그 해결 방법에 대해 설명합니다.
- 금속의 열처리란?
- 열처리에 의한 변형의 예(변태에 의한 체적 변화)
- 열처리 변형 문제에 대한 대책
- 기존에 발생했던 열처리 후의 변형 측정 과제
- 열처리 후의 변형 측정 과제의 해결 방법
- 요약: 측정하기 어려웠던 열처리 후의 변형 측정을 비약적으로 개선·효율화
금속의 열처리란?
금속의 열처리는 금속 재료를 가열·냉각하여 형태를 바꾸지 않고 성질을 변화시키는 가공 기술입니다. 변화시키는 성질에는 강도, 경도, 점도, 내충격성, 내마모성, 내부식성, 내식성, 절삭성, 냉간 가공성 등이 있으며 절단이나 소성 가공과 같은 금속 가공의 일종으로 분류됩니다.
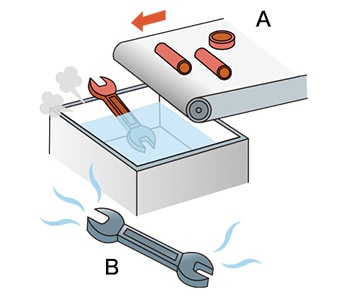
- A
- 달구기(금속이 적색이 될 때까지 가열)
- B
- 식히기(금속이 흑색이 될 때까지 냉각)
열처리에 의한 변형의 예(변태에 의한 체적 변화)
열처리에는 「담금질」, 「템퍼링」, 「어닐링」, 「노르말라이징」 등의 가공 방법이 있지만 이러한 가공 시 「변태」라는 현상이 발생합니다.
변태는 열처리에 의해 금속이 고체에서 액체, 액체에서 고체로 상태가 변화할 때 온도의 높낮이에 의해 결정 격자가 변화하여 존재 형태(조직)가 변화하는 것입니다. 변태에 조직이 바뀌면 체적도 변화하기 때문에 변형이 발생합니다.
예를 들어 공석강(탄소량이 약 0.8%인 강)을 상온에서 가열하여 오스테나이트 조직 상태로 만든 후 냉각하면 조직 변화에 의해 변형이 발생합니다. 그리고 변화 후의 조직은 냉각 방법에 따라 다르므로 변형의 크기도 냉각 방법에 따라 다릅니다.
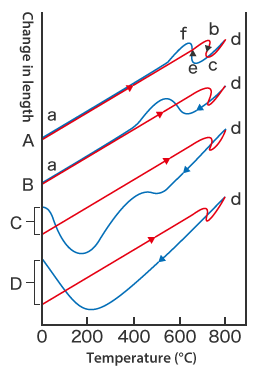
이 그래프는 냉각 방법에 따른 변형의 차이를 나타냅니다.
예를 들면 A(노내 냉각)의 경우 가열에 의해 열팽창하고(a→b), 가열 시 약 750℃ 부근(b→c)에서, 또한 냉각 시에는 약 730℃ 부근(e→f)에서 변태에 의한 치수 변화를 볼 수 있습니다.
또한 C(오일 냉각)와 D(수냉)에서는 각한 후에 분명한 길이 변화가 보입니다.
- A: 노내 냉각(서냉)
- 가열 후에도 용광로에서 꺼내지 않고 용광로 안에서 냉각하는 방법입니다. 시간당 약 30℃ 정도의 속도로 냉각합니다. 변태 후에는 펄라이트 조직이 됩니다.
- B: 공랭
- 가열 후 용광로에서 꺼내 상온에서 냉각합니다. 변태 후에는 솔바이트 조직이 됩니다.
- C: 오일 냉각
- 가열 후 기름으로 냉각하는 방법입니다. 일반적으로 약 60℃~80℃의 기름으로 냉각합니다. 변태 후 오스테나이트의 일부가 트루스타이트 조직이 됩니다.
- D: 수냉
- 약 40℃의 물로 냉각합니다. 변태 후에는 마르텐사이트 조직이 됩니다.
열처리 변형 문제에 대한 대책
열처리에 의한 변형 문제의 원인에는 앞서 설명한 변태에 의한 것 이외에 표면 형상이나 가열·냉각 등의 불비, 불균일 등이 있습니다. 여기에서는 이러한 현상과 원인, 그 대책에 대해 설명합니다.
담금질 균열
재료가 깨지는 현상입니다. 담금질 후 약 200℃ 이하로 냉각했을 때나, 담금질 다음날 등에 발생하는 경우도 있습니다.
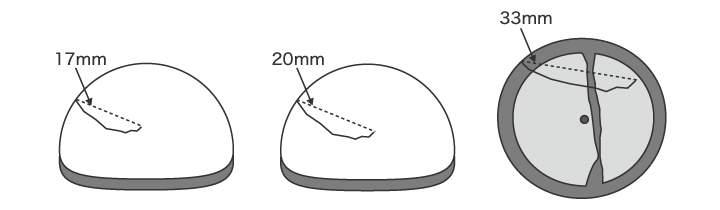
- 원인:
- 불균일한 가열이나 냉각에 의한 체적 팽창에 따른 형상 불량, 담금질 직후의 템퍼링의 미비, 나아가 담금질 온도가 너무 높은 것 등을 들 수 있습니다.
- 대책:
-
- 제품의 형상과 표면의 상태를 재검토한다.
- 담금질 후 냉각을 약 200℃ 이하로 하지 않는다.
- 담금질 직후에 템퍼링을 한다.
- 담금질 온도를 낮춘다.
연삭 균열
열처리 후 강재를 연삭 가공할 때 재료가 깨져 버리는 현상입니다. 「연마 균열」이라고도 합니다. 연삭 균열에는 2종류가 있으며 절삭이나 연마 등의 가공으로 표면 온도가 약 100℃까지 상승했을 때에 발생하는 것을 「제1종 연삭 균열」, 약 300℃까지 상승했을 때에 발생하는 것을 「제2종 연삭 균열」이라고 합니다.
-
제1종 연삭 균열
-
제2종 연삭 균열
- 원인:
- 잔류 오스테나이트가 마르텐사이트로 변태되면 팽창합니다. 이 팽창에 의한 응력으로 균열이 발생합니다. 또한 절삭이나 연마 등의 가공으로 표면 온도가 약 650℃~850℃로 가열되었을 때에도 발생합니다.
- 대책:
-
- 적절한 템퍼링을 실시한다.
- 연마의 마찰에 의한 발열을 억제한다.
담금질 변형
열처리에 의해 발생하는 강재의 변형으로 담금질·템퍼링 중 열팽창 수축에 의한 「열변형」과 조직 변화에 의한 「변태에 따른 체적 변화」가 있습니다.
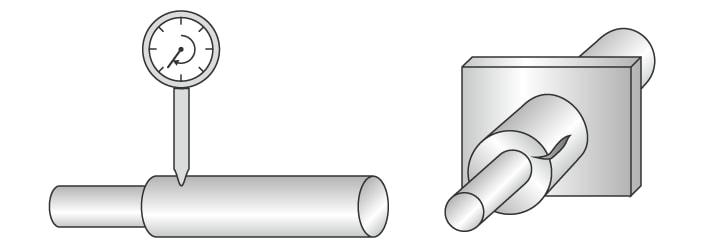
- 원인:
- 가열·냉각의 불균일, 급속 가열, 급속 냉각, 부분적인 두께의 불균일이 원인입니다. 복잡한 형상의 경우에는 부품 내부의 온도 불균일 등으로 인해 발생합니다.
- 대책:
-
- 균일한 가열, 냉각 처리가 가능하도록 형상을 다시 고친다.
- 가열·냉각 속도를 느리게 한다.
기존에 발생했던 열처리 후의 변형 측정 과제
열처리 후 치수와 형상이 공차 내에 있는지 확인하는 것은 매우 중요합니다. 특히 복잡한 형상의 제품인 경우, 정밀하고 정량적인 3D 형상의 측정이 요구됩니다.
지금까지 열처리 후의 변형 측정은 윤곽 형상 측정기 또는 3차원 측정기로 실시해 왔습니다. 그러나 기존의 3차원 측정기나 윤곽 형상 측정기 등의 경우 정확하게 측정하기에는 난이도가 높고 편차가 생기는 등 여러가지 과제가 있었습니다.
윤곽 형상 측정기를 이용한 변형 측정 과제
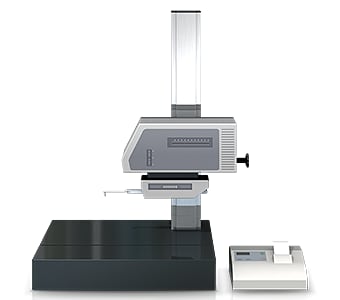
윤곽 형상 측정기는 스타일러스라고 하는 프로브를 이용하여 대상 물체의 표면을 덧그림으로써 그 윤곽 형상을 측정, 기록하는 장치입니다. 최근에는 프로브 대신 레이저를 이용하여 비접촉으로 윤곽을 스캔함으로써 복잡한 형상을 측정할 수 있는 기종도 있습니다. 또한 기종에 따라서는 상하 양면을 측정할 수 있는 것도 있습니다.
윤곽 형상 측정기를 사용할 때에는 측정 포인트에 대해 정확하게 측정 라인을 맞추어야 합니다.
그래서 다음과 같은 과제가 있었습니다.
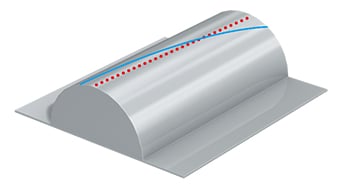
- 시료를 지그에 고정하거나 레벨링 등의 작업을 진행하는 데에 시간이 걸립니다. 또한 정확한 레벨링을 위해서는 윤곽 형상 측정기에 관한 지식이나 스킬이 필수적으로 요구됩니다.
- 윤곽 형상 측정기의 프로브는 프로브 암 지점을 중심으로 하 원호 운동을 하며, 프로브 선단 위치는 X 방향으로도 이동하기 때문에 X축 데이터에도 오차가 발생합니다.
- 목표했던 대로 프로브를 통과시키는 작업은 매우 어려우며, 미묘한 프로브의 어긋남이 측정값 편차의 원인이 됩니다.
- 특정 위치를 조준하여 측정해야 하므로 N수를 늘리기 어렵습니다.
- 일부 측정값만 받아볼 수 있기 때문에 때문에 면에서의 평가를 할 수 없습니다.
3차원 측정기를 이용한 변형 측정 과제
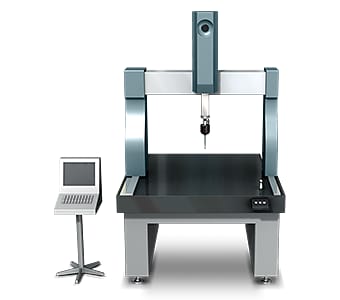
일반적으로 3차원 측정기에서는 측정 항목에 프로브를 대고 덧그리는, 「스캐닝」이라는 방법으로 측정합니다. 스캐닝 측정은 일정한 피치에서 여러 점을 측정합니다.
이 측정 방법에는 다음과 같은 과제가 있습니다.
- 원통의 중심이나 굴곡을 수직으로 지나는 선, 원의 중심을 지나는 선 등 원하는 곳으로 프로브가 지나도록 하는 것은 매우 어렵습니다. 또한 중심 각도가 얕은 각 R의 경우 짧은 원호에서 원주 전체를 산출하기 때문에 미세한 측정 오차가 크게 확대됩니다. 이렇게 측정 항목이 어긋남으로써 미묘하게 값의 편차가 발생하는 경우도 있습니다.
- 작은 부분의 3차원 형상을 측정하는 경우 프로브를 측정 위치에 맞추지 못할 수 있습니다. 또한 측정 정밀도는 측정할 점과 선의 수에 비례하므로 많은 부분을 측정해야 합니다.
이와 같이 현장의 모든 사람이 정확하게 측정할 수 있는 것은 아니고 측정할 수 없는 부분도 있으며 측정기의 설치 장소도 한정되는 등 큰 과제가 있었습니다.
열처리 후의 변형 측정 과제의 해결 방법
기존에 사용되고 있는 일반적인 측정기는 대상 물체의 고정에 시간이 걸리고 입체적인 대상 물체·측정 항목을 점이나 선으로 접촉하면서 측정한다는 과제가 있습니다. 이러한 측정 과제를 해결하기 위해 KEYENCE에서는 원 샷 3D 형상 측정기「VR 시리즈」를 개발했습니다.
대상 물체의 3D 형상을 비접촉 방식을 이용하여 면으로 정확하게 포착할 수 있습니다. 또한 스테이지의 대상 물체를 최고 속도 1초 만에 3D 스캔함으로써 3차원 형상을 고정도로 측정할 수 있습니다. 이로 인해 측정 결과의 편차 없이 순간적으로 정량 측정할 수 있습니다. 여기에서는 구체적인 장점을 소개합니다.
장점 1: 최고 속도 1초만에 다점 측정 가능
「VR 시리즈」는 원 샷 최고 속도 1초만에 대상 물체의 3D 형상을 면(80만점의 데이터)으로 측정할 수 있기 때문에 지금까지 다점 측정에 걸렸던 시간을 비약적으로 단축합니다. 대상 물체 표면 전체의 최대·최소 요철을 순식간에 정확하게 측정해 설정해 놓은 공차로 대상 물체의 모든 부분을 신속하게 평가할 수 있습니다.
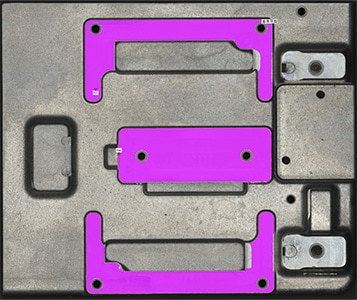
또한 한 번 대상 물체를 스캔해 두면 과거에 측정했을 때와는 다른 부분의 프로파일(단면 형상)을 측정하는 것도 가능합니다. 동일한 샘플을 번거롭게 다시 준비한 후 재측정할 필요가 없습니다.
장점 2: 기준 데이터와 측정 데이터를 비교할 수 있다.
「VR 시리즈」의 장점은 효율적인 데이터 수집만이 아닙니다. 측정 데이터를 목록으로 표시할 수 있는 것은 물론 모든 데이터에 같은 해석 내용을 일괄 적용하는 것이 가능합니다.
예를 들면 복수의 대상 물체의 형상을 측정해 열처리 전과 열처리 후의 데이터의 차이나 기준품과 비교해 NG품에 얼마나 차이가 있는지 등을 한눈에 확인할 수 있습니다. 이로 인해 열처리로 인한 변형의 정량적인 분석·평가를 간단하게 실현할 수 있습니다.
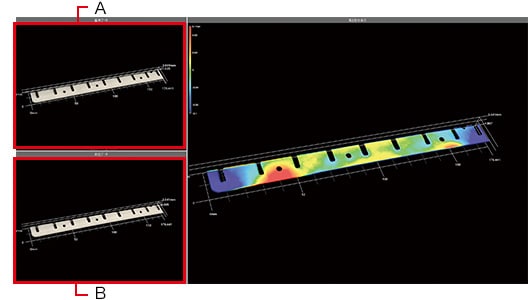
- A
- 기준 데이터
- B
- 측정 데이터
또한 지금까지 많은 수고와 시간이 필요했던 복잡한 형상의 대상 물체도 신속하게 측정할 수 있습니다. 또한 측정 결과는 모두 데이터화되기 때문에 이후의 데이터 비교나 해석 작업의 수고도 크게 줄일 수 있습니다.
요약: 측정하기 어려웠던 열처리 후의 변형 측정을 비약적으로 개선·효율화
「VR 시리즈」라면, 시간이 걸려서 측정하지 못했거나 열처리에 의해 형상이 복잡하게 변화하여 측정할 수 없었던 제품도 신속하게 측정하여 정량화할 수 있습니다. 이로 인해, 더욱 효율적이고 높은 수준의 품질 평가를 실현할 수 있습니다.
- 면에서 측정하므로 동시에 다점 데이터를 취득할 수 있으며, 복잡한 형상의 측정 시간을 큰 폭으로 줄일 수 있습니다.
- 여러 개의 측정 데이터를 목록으로 비교할 수 있어 다양한 열처리에 의한 변형 차이를 파악·해석할 수 있습니다.
- 사람에 의한 측정값의 편차를 해소하여 정량적으로 측정할 수 있습니다.
- 위치 결정 등의 작업 없이 스테이지에 대상 물체를 놓고 버튼을 누르기만 하면 되는 간단한 조작을 실현했습니다. 특정 작업자만 측정 업무를 할 수 있는 문제를 해소합니다.
- 간단·고속·고정도로 3D 형상을 측정할 수 있기 때문에 단시간에 많은 대상 물체를 측정할 수 있어 품질 향상에 도움이 됩니다.
그 외에도 과거의 3D 형상 데이터와의 비교, 거칠기 분포 등을 간단하게 분석할 수 있기 때문에 온도에 의한 파단면 상태의 경향 분석, 파괴 상태의 확인 등 다양한 용도로 활용할 수 있습니다.